
Engineering outside the box
Visiometa stands for process stability and efficiency in the foundry business. Our method relies on the precise modeling and visualization of the casting process using the most advanced technology. Our products and services provide significant time and cost savings combined with high planning accuracy. The emphasis is on the technical and commercial evaluation of the process and the production-related design optimization of the casting.
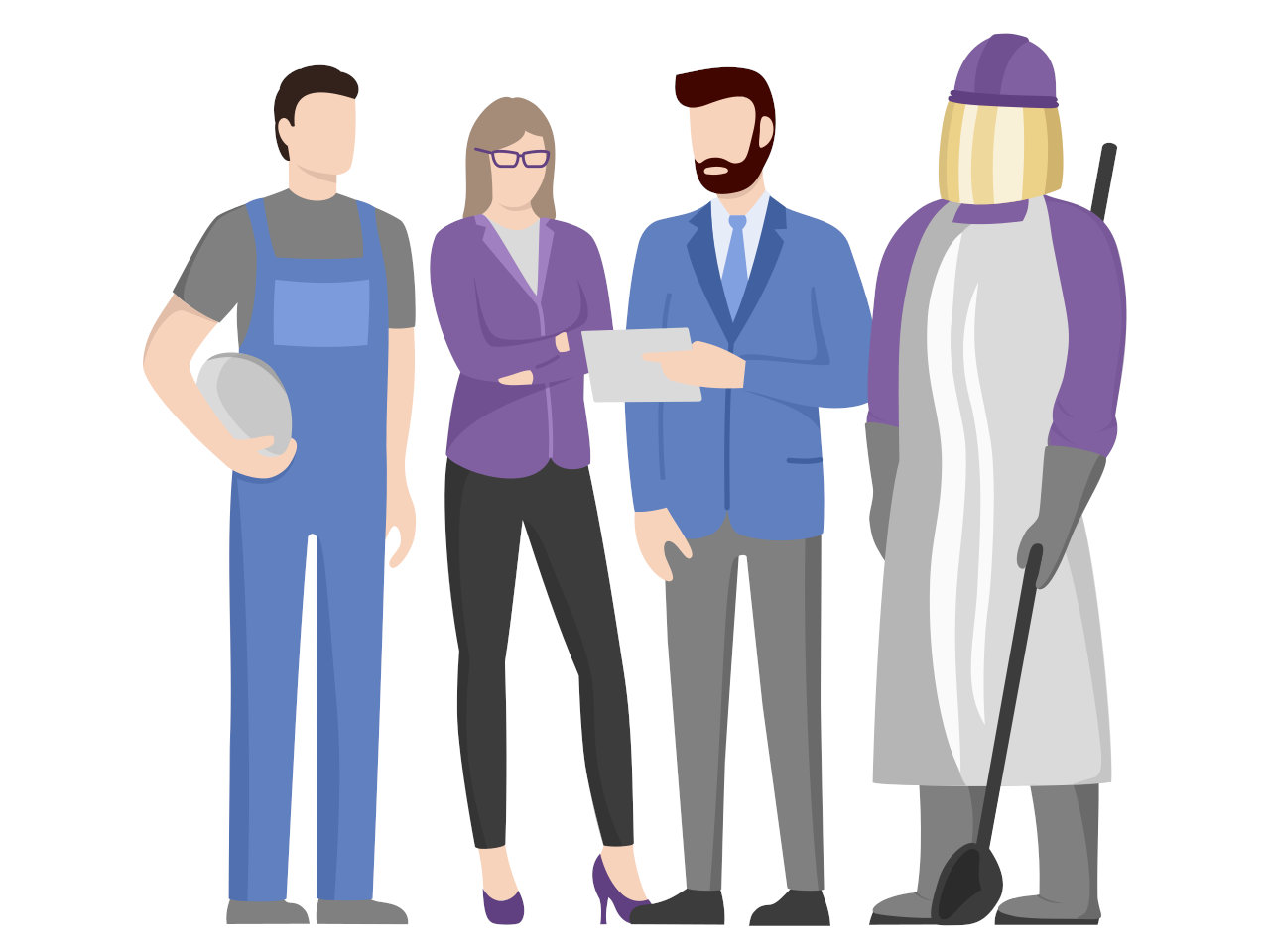
We're here to serve you - whether you're making one-off prototypes or a million parts in high volume production. Our expertise covers everything from the smallest light metal parts to iron heavyweights in the high tonnage range.
Our engineering team has many decades of experience with international foundry projects involving all relevant process types. We will gladly support your enterprise with our knowledge and proficiency. Please contact us!
Process Planning
The most complete information available, its correct utilization and lossless communication are the foundations for every decision within resilient process planning. Technical principles, clear visualizations and integrated validation are decisive aspects of meeting this high standard.
Modulus Analysis
Within a very short time, a product reveals its solidification behavior in the mold through its local modulus field. This information opens up access to viable concept ideas, especially with regard to the casting orientation and the layout of gating and feeding system.
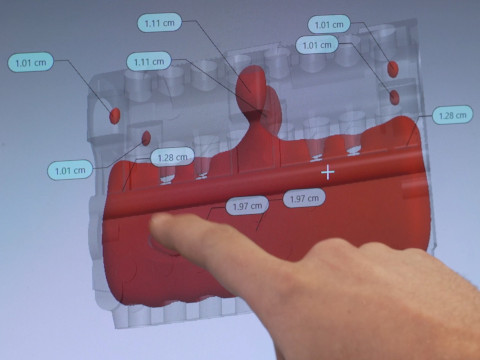
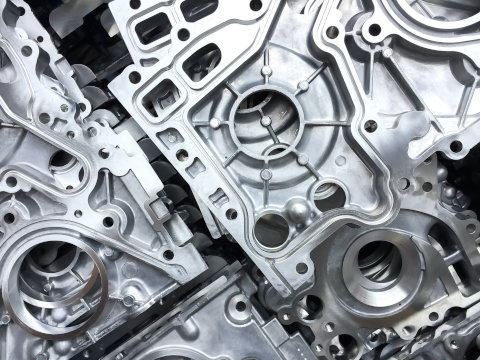
Proper Casting Design
The most common casting defect is the shrinkage hole. In order to saturate every hotspot within the cast part from the feeding system, controlled solidification is essential. Generally, the functional design does not meet this requirement, which is why adapting the part to the casting process is so important.
Mold Design
Optimal mold design requires complex considerations that go beyond mere functionality. In the case of a sand mold, the greatest possible coverage of the parting surface with cavities can decisively impact economic efficiency. Permanent molds, on the other hand, have to meet special requirements with regard to their quasi-stationary temperature field during production.

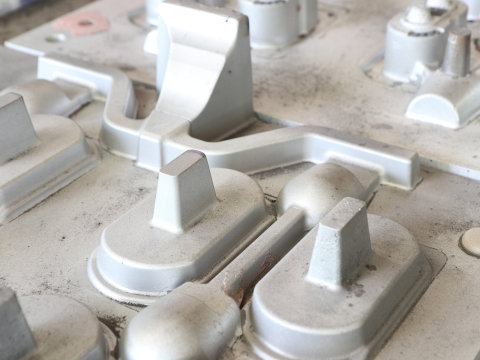
Layout of the Gating System
In terms of fluid mechanics, liquid metals behave like Newtonian substances and thus, in principle, similar to water. However, the design of the gating system is not only about complying with the laws of physics, but also about the correct pouring time and the resulting temperature distribution within the cavity.
Process Simulation
Every casting process with its corresponding geometric models and procedural operations is initially just a preliminary concept that requires validation before it can be implemented. The computer-aided simulation of mold filling and solidification has made this possible for metal casting in an entirely virtual way.
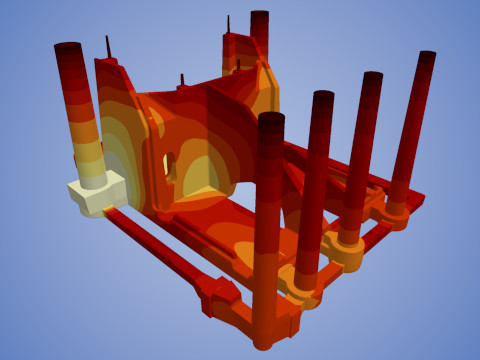
Optimization and troubleshooting
The complexity of metal casting can never be completely mastered. That is why a comprehensive analysis of the real process is of great importance. The knowledge gained not only leads to the rapid elimination of flaws and defects, but also generates valuable experience for future projects.
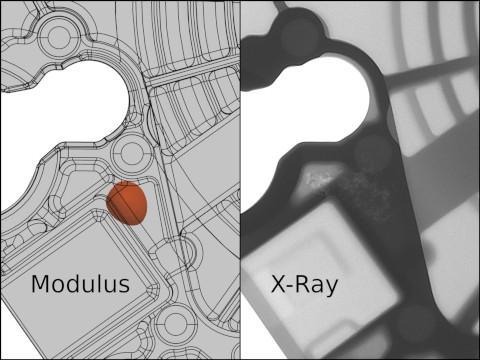
Defect and Root Cause Analysis
If not all castings meet the customer's requirements, the first and most important step is to identify the defects that cause the rejection of the affected products. Only accurate defect classification and understanding of the causation mechanism will lead to measures that eliminate or at least mitigate the defect event.
Weak Point Analysis
Scrap and rework costs result from shortcomings mainly within the actual casting process. The most common three of all possible casting defects are shrinkage holes, non-metallic inclusions and incomplete filling. The combination of real and virtual weak point analysis is the source of reliable information that enhances the core process and thus the yields achieved.
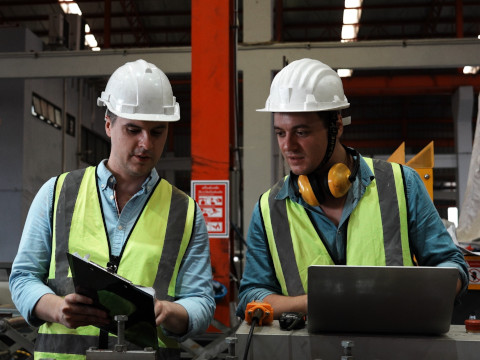
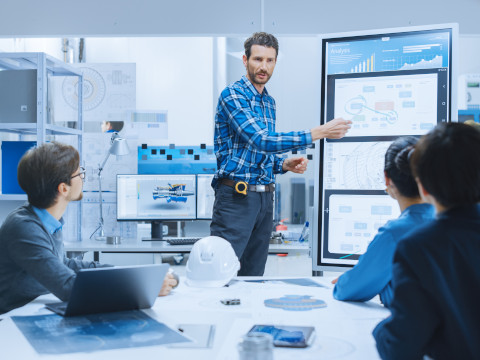
Productivity Assessment
The management of complex processes requires a high level of information acquisition and evaluation in connection with the qualitative and quantitative production output. The experience and knowledge gained are the foundation for future projects and satisfied customers.
Training and Education
Continuous development, introduction of innovations, fundamental understanding and individual experience are all prerequisites for the successful management of casting processes. They culminate in synergies when change and refinement transform the workforce into a strong community.
Foundry Technology
Metallurgy, machinery, tooling and process engineering, complemented by deeper insights from experienced foundry experts, enrich the thinking of decision makers at all levels. In seminars of one to several days, practice-oriented specialist knowledge on sand casting, permanent mold casting and investment casting processes is conveyed.
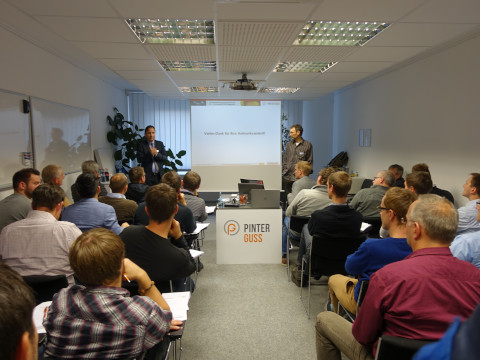
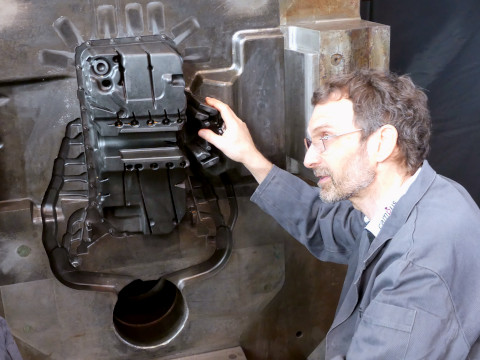
Staff Qualification
Theoretical basics combined with practical experience bring out competence, know-how and a sense of responsibility in the workforce. Direct and active training on the shopfloor deepens the learning effect beyond the auditory and visual reception of information in the seminar room.
Process Management
Only systematic analysis of the process reveals the potential for improvement and optimization. Standardization of applied methods and procedures makes the results of successful projects reproducible. Experienced professionals guide participants to think and act independently using the control loop technique (PDCA).
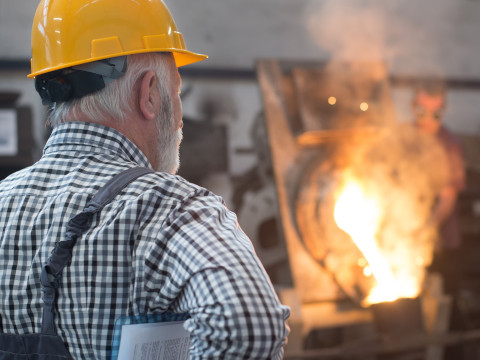
Do you have any questions?
Contact us!
There is no charge for asking! We look forward to hearing from you soon.
Direct Message
Use our online form to submit your request quickly and easily.
+49 (0) 2971 961 98 91
Mondays to Fridays
08:00 to 18:00 CET
info@visiometa.com
Send us an email and we will get back to you promptly.
Visiometa GmbH
Zur Parmke 14
57392 Schmallenberg
Germany