An important aspect of castability is the inherent quality of a casting to solidify in a controlled manner. If the part contains inner areas that solidify in isolation, it may no longer be possible to compensate for the volume deficit caused by shrinkage. Without the use of feeders and other aids, casting defects will then occur.
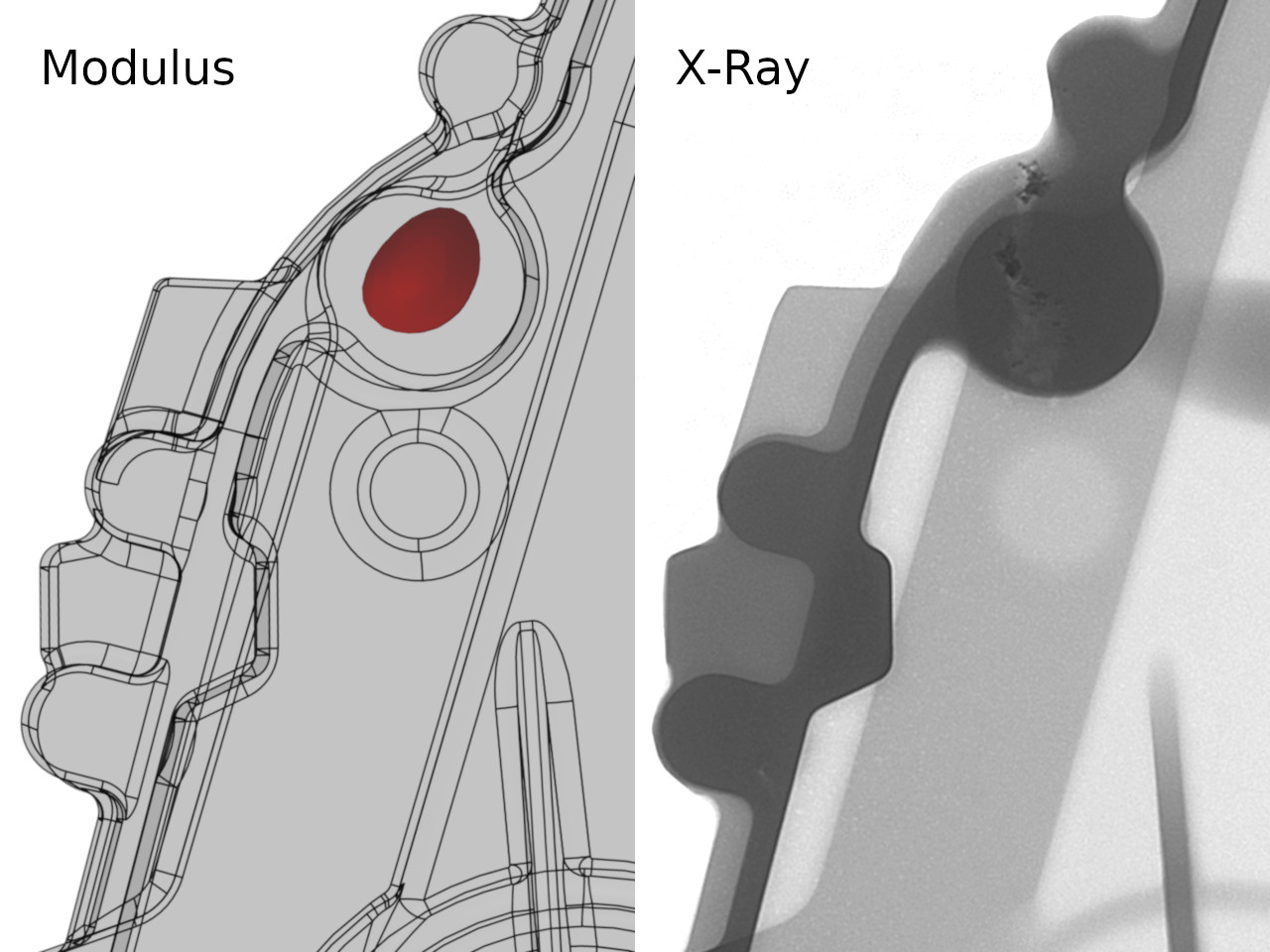
Areas of isolated solidification can be detected at an early stage by means of a temperature field analysis. To this end, the solidification process must be physically simulated. However, this procedure is not only time-consuming, it also does not provide any concrete indication as to the optimum design of feeders or chills.
Alternatively, as a direct method, using the solidification modulus has proven successful for decades. The modulus is proportional to the solidification time, while representing a measure of length. This means that feeders, for instance, can be dimensioned directly on the basis of the calculated values.
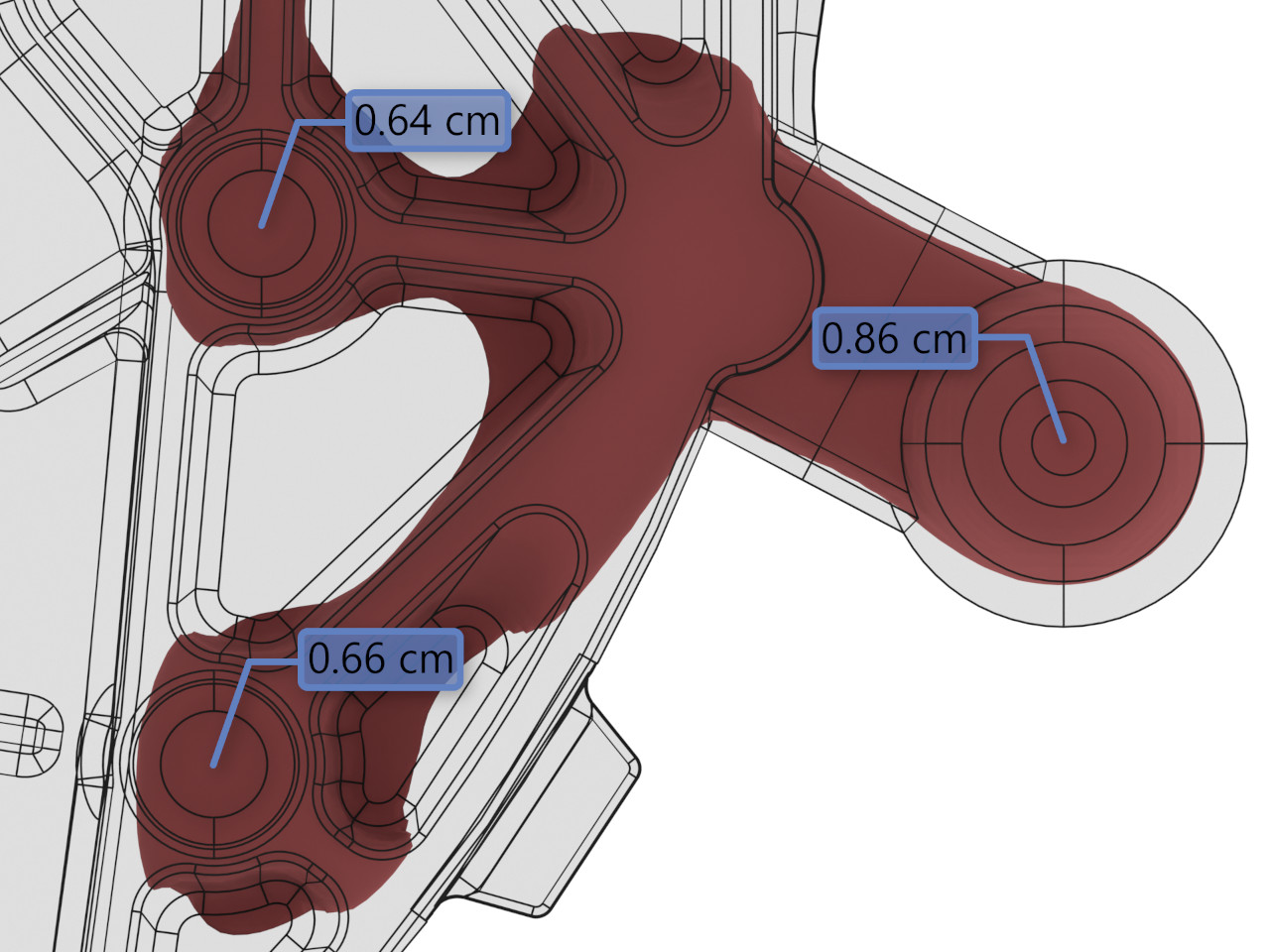
Calculation of the modulus in Visiometa is amazingly simple and extremely fast. The analysis of the casting is performed in three basic steps:
- Importing and arranging geometric models.
- Generating a suitable discretization.
- Starting the actual calculation.
The entire process takes only a few seconds in practice, usually up to a few minutes for very complex parts. No previous knowledge of simulation technology or CAD is required.
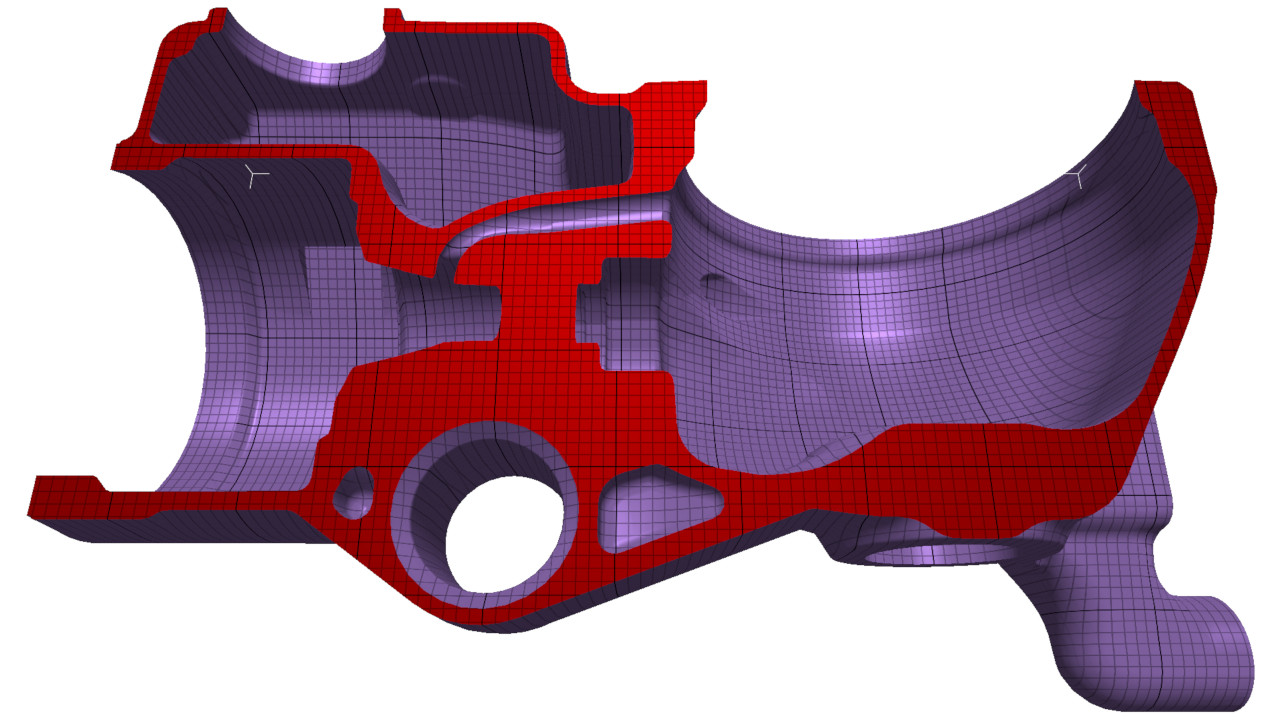
Once the calculation is done, the modulus values can be displayed, for example, by projection onto the model surface. In combination with Visiometa's real-time clipping, users can get an impression of the qualitative solidification behavior of the casting. Sand edge effects are particularly well represented in this way.
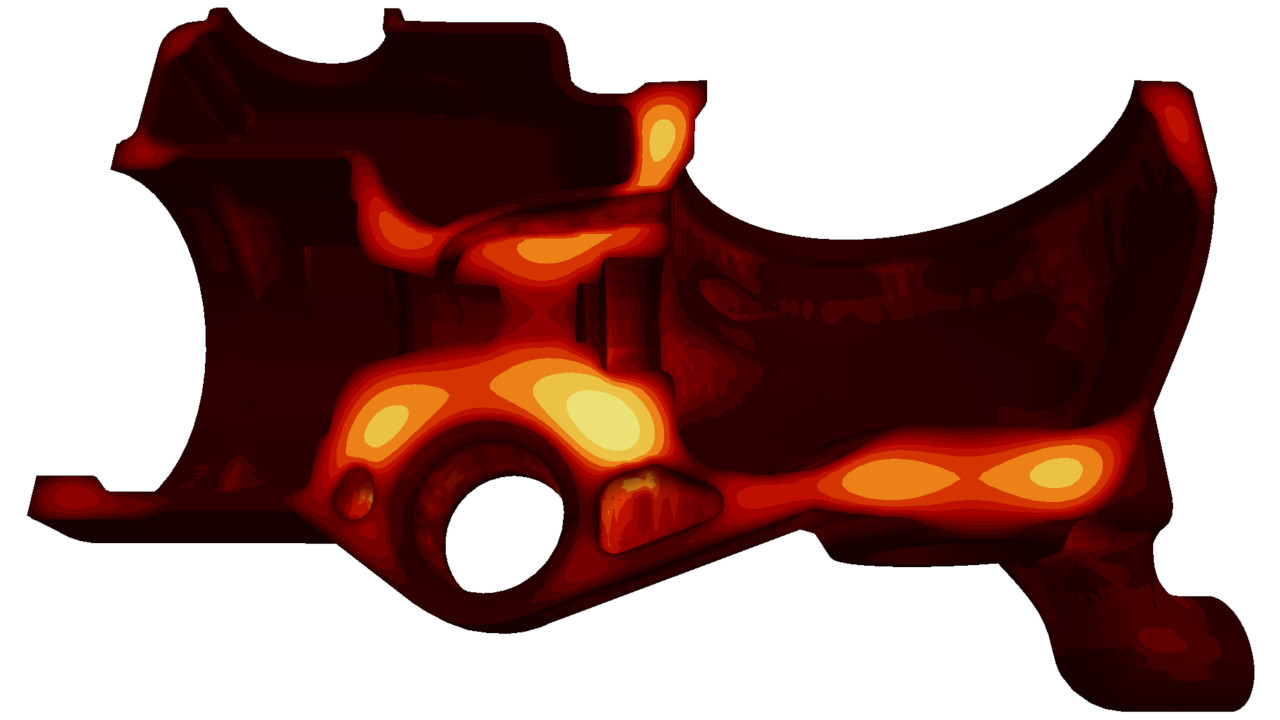
A more advanced visualization technique is the so-called isosurface. Users first set a threshold value for the modulus. The software then calculates the surface of all regions that exhibit the same or a higher modulus value. In this way, the solidification dynamics can be more easily understood. Areas of isolated solidification now stand out clearly as separate bubbles or constrictions.
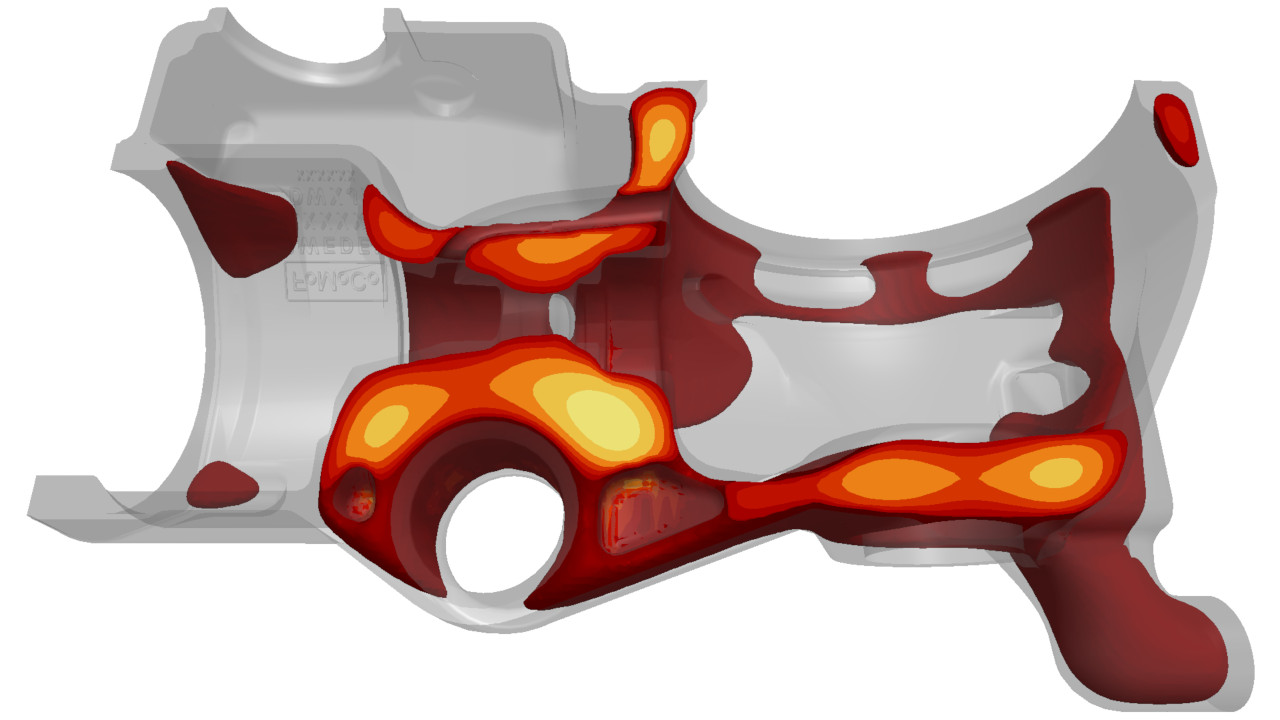
To further simplify the process of finding these problem areas, Visiometa offers an automatic hotspot detection. At the push of a button, the entire component can be scanned for local extreme values of the modulus. With this feature, the user will not miss any potential shrinkage defect, no matter how hidden and inconspicuous. The corresponding modulus values are presented directly as annotations to the scalar field.